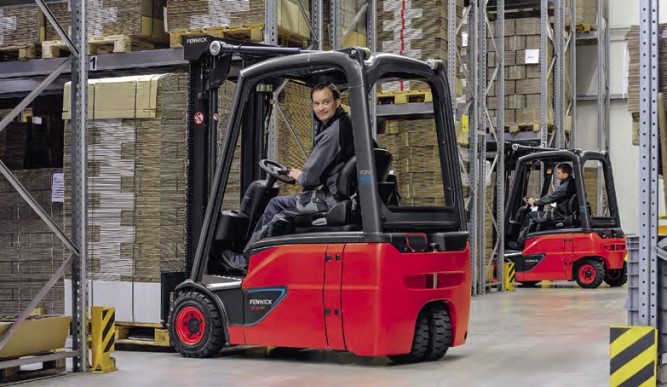
©
Fenwick
Entrepôts
Avec Fenwick, DS Smith passe durablement au lithium-ion
Sur ses sites de Toury et Neuville-aux-Bois, DS Smith Packaging France a récemment renouvelé son parc de chariots, poursuivant sa collaboration historique avec Fenwick- Linde. L’occasion pour le fabricant d’emballage carton de faire évoluer ses véhicules vers la technologie lithium-ion pour plus de flexibilité et moins de risques d’utilisation.
C’est une collaboration forte et sur le long terme que Fenwick-Linde et DS Smith mènent depuis maintenant plus de 20 ans. Si le fabricant d’emballage carton collabore avec d’autres partenaires pour ses activités en France, le constructeur franco-allemand reste son principal fournisseur de véhicules, avec une part de marché de près de 60 % sur ses 30 usines françaises. Il y a un peu plus de deux ans, DS Smith fait le choix de renouveler en profondeur son parc sur certains sites : « Nous menions alors de grands projets d’investissements et de réorganisation industrielle à l’occasion desquels nous avons réétudié nos flux internes. Cela nous a amenés à revoir notre parc existant », explique Nicolas Cipierre, directeur des sites de Toury (28) et Neuville-aux-Bois (45), dédiés à la fabrication d’emballage en carton ondulé.
Une réflexion que DS Smith a pu mener avec son partenaire Fenwick : « Un parc de véhicules doit être réévalué régulièrement et nous réalisons des revues de nos besoins une à deux fois par an avec Fenwick ». À l’issue des échanges, décision est prise de ne pas faire évoluer significativement la quantité ou le type de chariots déployés en leasing sur ces deux sites, c’est-à-dire principalement des véhicules frontaux de moyen tonnage avec pince pour bobine de papier dans certains cas. « Des optimisations avaient déjà été faites sur ce sujet-là avec Fenwick par le passé », précise Nicolas Cipierre. Cependant, une nouveauté technologique émerge assez vite dans les échanges et attire l’intérêt de DS Smith pour renouveler sa flotte : le passage vers des batteries lithium-ion en lieu et place de celles au plomb. « Le lithium-ion nous ouvrait un champ de possibilités côté réimplantation de nos ateliers. Dans les études de flux sur nos deux sites, nous avions un certain nombre de contraintes liées aux locaux de charge, qui prennent beaucoup de mètres carrées au sol et ont des obligations règlementaires non négligeables – rétention, extraction de gaz, contrôle de niveau d’hydrogène, etc. De plus, changer une batterie plomb n’est pas un process anodin : il faut des moyens de manutention, et mobiliser une ou deux personnes. La problématique de la pénibilité sur le changement des batteries plomb était une thématique récurrente ces cinq dernières années au sein de notre organisation. Face à ces impératifs, la technologie lithium-ion nous affranchit d’un certain nombre de contraintes, ce qui justifie son prix plus élevé », raconte Nicolas Cipierre. « Il faut penser en coût complet : nous ne regardons pas que la part location et maintenance, mais aussi la part énergie et économie pour l’usine et son organisation », ajoute François Bouville, regional logistic category manager chez DS Smith.
Un confort d’utilisation « incomparable »
Concrètement, sur site, l’implantation du lithium-ion a permis de supprimer l’un des deux locaux de charges pour batterie. À la place, des postes de recharge ont été installés dans les bâtiments, permettant de rapprocher les lieux de charge des endroits où les chariots élévateurs étaient utilisés. « Nous avons des sites de 2 000 m2 où il était est impossible de multiplier les locaux de charge. Avec le lithium-ion, nous avons installé de nouvelles lignes électriques pour pouvoir charger à proximité de nos magasins de produits finis et de nos expéditions, juste à côté des zones de vie et de travail de nos caristes quand ils ne sont pas en train de conduire », précise Nicolas Cipierre.
« Aujourd’hui, nous ne pourrions pas réintroduire des batteries plomb dans nos ateliers tant les gains sont nombreux en termes de qualité de vie au travail ». La gestion par biberonnage a aussi permis de réduire le nombre de batteries : « Là où nous avions deux batteries par chariot, voire plus, nous n’en avons plus qu’une en lithium-ion », souligne Nicolas Cipierre. « Le confort d’utilisation est incomparable et la durée de vie de ces batteries reste très fiable, à l’inverse d’une batterie plomb qui pouvait se dégrader en cas de mauvaise utilisation ».
Un nouveau standard qui pourrait être déployé sur d’autres sites
Cette mutation du parc se déroule depuis maintenant deux ans sur les sites de Toury et Neuville-aux-Bois. « Dans le cadre de notre partenariat avec Fenwick, nous avons pu faire des renouvellements anticipés pour des chariots qui arrivaient au terme de leur contrat, afin de pouvoir basculer plus rapidement vers le lithium-ion. C’est la raison pour laquelle le site de Neuville-aux-Bois a pu aller plus vite sur le sujet que Toury, où le renouvellement sera complété d’ici la fin de l’année, nous permettant d’avoir un site 100 % équipé en lithium-ion », souligne Nicolas Cipierre. Aujourd’hui, la technologie est donc devenue un standard au sein de ces deux sites, les premiers chez DS Smith. Une stratégie qui est également en cours de réflexion ailleurs dans le groupe comme le précise François Bouville : « À l’avenir, le lithiumion sera étudié sur nos autres usines en France en fonction des besoins lors du renouvellement. Cependant, les engins au lithium-ion doivent être très utilisés pour être rentables – difficile donc de les proposer sur de petits sites où les véhicules ont des taux d’utilisation plus faibles. Pour certaines usines, il faudra trouver un équilibre : avoir du lithium-ion pour les cartonneries qui tournent en trois-huit, mais des batteries classiques pour l’expédition par exemple, qui a des plages horaires plus réduites ».
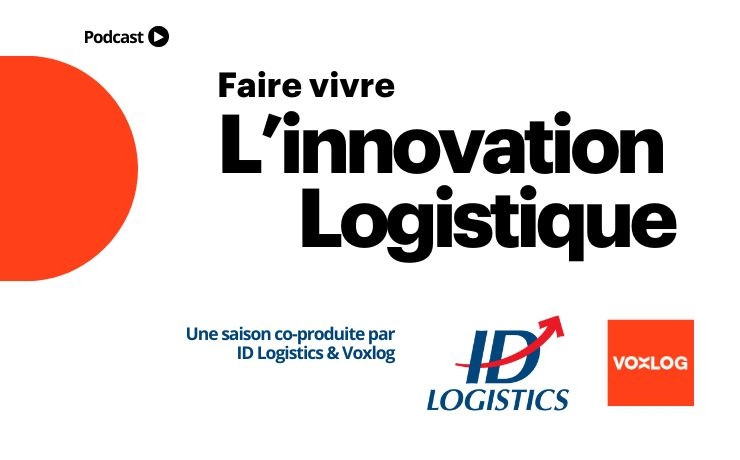