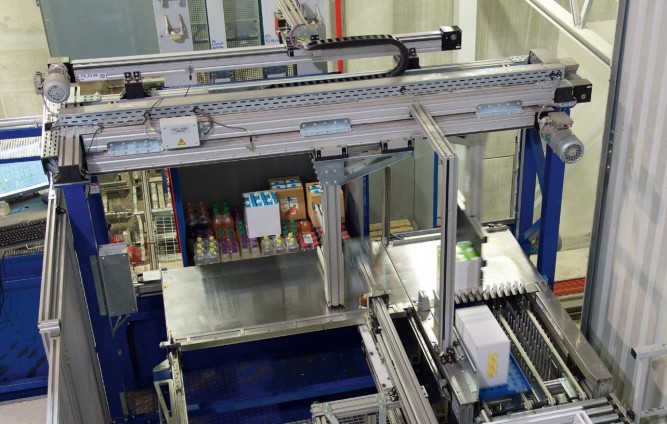
©
Witron
Entrepôts
La Scapalsace continue de s'appuyer sur les solutions de Witron
Mis en service en 2014, le système automatisé de la centrale d’approvisionnement Scapalsace de E. Leclerc – installation pionnière en France – a su répondre aux défis de l’enseigne : multiplication des magasins, volumes grandissants... Retour sur les atouts de cette installation avec Saïd Bindou, ancien directeur de la centrale passé adhérent, et artisan du projet.
Voilà maintenant plus de six ans que la centrale d’approvisionnement Scapalsace de E. Leclerc, située à Colmar (68), s’appuie sur les solutions automatisées de Witron pour assurer la logistique de ses magasins dans les départements de l’Est de la France et en Bourgogne. Une installation de pointe qui a été la première collaboration entre l’enseigne et le constructeur allemand, suivie ensuite par des projets similaires au sein du mouvement E.Leclerc : Scapest, Scapnor, Scapartois, Socara et Socamil. Démarré en 2014 après un travail conjoint de Witron et E. Leclerc, le système traite aujourd’hui 210 000 colis par jour et tout le spectre des 13 000 références de produits de grande consommation secs, à lente ou forte rotations. L’OPM (Order Picking Machinery), piloté par les WMS et WCS développés par Witron, propose une automatisation complète allant du stockage avec dépalettisation automatique, jusqu’à la préparation de commandes, avec mise à disposition sur les quais des palettes destinées aux magasins et aux drives et des séquences de chargements pour minimiser les camions sur les routes.
De nombreux avantages pour les adhérents
Acteur majeur de ce projet précurseur pour la grande distribution alimentaire en France, Saïd Bindou est l’ancien directeur de la Scapalsace. C’est lui qui, au début des années 2010, est à l’origine du travail d’automatisation de la centrale, et c’est lui qui le pilotera aux côtés de Witron. Ayant été promu adhérent E. Leclerc à Strasbourg, il est aujourd’hui à la tête d’un hypermarché, un supermarché ainsi que deux drives. « Si j’ai été l’initiateur du système, j’en suis aujourd’hui le client, côté magasin », résume-t-il. L’ancien directeur de la Scapalsace note les multiples bénéfices offerts par la solution. En tête, sa rentabilité économique, mais aussi sa fiabilité et la qualité de la préparation, à laquelle il est désormais attentif en tant qu’adhérant : « Depuis le lancement de l’installation en 2014, la centrale n’a jamais failli dans sa qualité de service aux magasins. L’outil a toujours su absorber les besoins, même en période de crise. Nous n’avons jamais eu de rupture. La qualité est également un point clé. Les palettes qui arrivent dans nos magasins n’ont aucune casse. De plus, elles sont directement préparées dans l’ordre des rayons par l’algorithme de palettisation, ce qui facilite le rayonnage en magasin ou drive. In fine, c’est un gain de temps, et donc un avantage économique. Notre ROI, axé sur les conditions de travail, l’ergonomie ou la performance ne tenait pas compte de ce paramètre, jugé difficile à remplir et estimé comme un éventuel plus. Mais la solution le réalise au quotidien pour chaque point de vente ».
Du côté du transport également, les avantages sont nombreux. En effet, le module de préparation automatisé permet la réalisation de palettes d’une hauteur de 1,20 mètre, taille complexe à atteindre avec des process manuels. Ce format permet ainsi de faire des chargements en « double lisse » dans les camions, permettant de réaliser des économies importantes pour les adhérents. « Le taux de remplissage des camions a été augmenté de 20 à 30 %, ce qui a permis notamment une réduction du niveau des émission de CO2 », souligne Saïd Bindou.
Un système capable d’évoluer avec les besoins
L’installation automatisée de la Scapalsace a su répondre aux évolutions de la centrale dès son lancement. « Nous avons eu l’opportunité d’intégrer un certain nombre de magasins qui faisaient partie du groupe Coop Alsace, soit une quinzaine de sites générant 30 % de volumes supplémentaires », se souvient Saïd Bindou. Witron a ainsi déployé très rapidement deux lignes supplémentaires dans un entrepôt déjà opérationnel pour répondre à ces besoins. Et au fil des années, le site a absorbé l’augmentation des points de ventes, et tout particulièrement des drives, en fort développement. « Nous sommes passés d’une cinquantaine de points de livraison à une centaine. Cela a été permis par le rajout de machines supplémentaires et puis, au fur et à mesure, par l’utilisation de la solution sur une plus grande plage horaire. Plus généralement, au fil des années, la performance même du site a augmenté grâce à notre expérience. Le coût global de la centrale est d’ailleurs en baisse progressive. Bien évidemment, il y a des limites et d’ici deux ou trois ans, avec une croissance comme la nôtre, il sera nécessaire de rajouter un investissement supplémentaire, sachant que le premier est déjà largement optimisé », note Saïd Bindou.
Une nécessité de poursuivre les investissements, démontrée lors de la crise du Covid-19, ayant entrainé de fortes demandes pour la grande distribution. « Nous avons pu passer cette crise en poussant l’installation au maximum de ses capacités, avec un travail continu sur des journées de 22 heures (au lieu de 18 à 20 heures en moyenne). Les retards ont été minimes et nos magasins ont tous pu être livrés, ce qui aurait été impossible avec une logistique conventionnelle ». Des réflexions sont ainsi d’ores et déjà en cours au sein de la centrale afin d’aller vers une installation similaire pour les produits frais, dans un autre bâtiment à proximité. Fonctionnant encore sur une logistique conventionnelle avec un système de trieur crossbelt, ce segment bénéficiera prochainement de l’installation d’un tout nouveau système FPM (Flow Picking Machinery) de Witron, proposant un picking des colis en flux tendu sans stock, afin de soutenir l’activité de la Scapalsace et son développement. Quitte à y intéger d’autres typologies de produits si besoin est : « Il est possible d’envisager une installation légèrement surdimensionnée pour les produits frais qui serait capable d’accueillir également une partie des produits secs en cas de pic d’activité », estime Saïd Bindou.
À lire également :
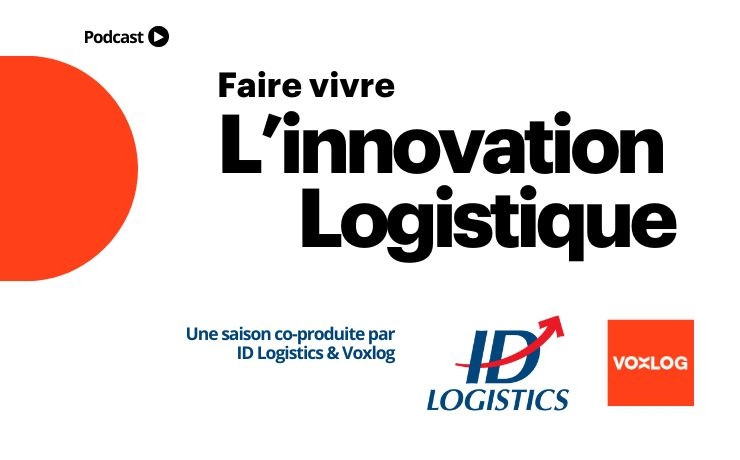