Chargeurs
ITM Lemi automatise la supply chain des petits produits de Bricomarché et Bricorama
Sur son site de Garancières 1 en Eure-et-Loir, ITM Lemi, société logistique filiale du groupement Les Mousquetaires, s’est équipée depuis deux ans d’une solution automatisée pour la gestion de ses petits produits. Une installation de pointe qui répond aux besoins nouveaux de l’entreprise, notamment liés à la récente intégration de l’enseigne Bricorama.
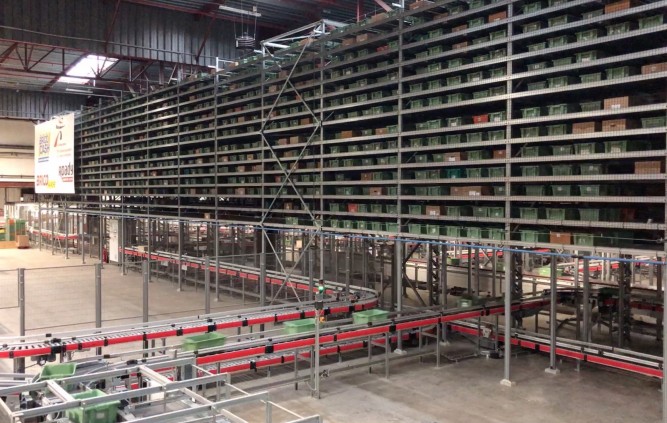
©
Voxlog
Si la grande distribution alimentaire est sans doute la plus connue des activités des Mousquetaires, le grand groupe français présente également un important réseau de magasins dans le domaine des équipements de la maison et du bricolage, avec ses enseignes Bricomarché, Bricocash ainsi que Roady (pour l’équipement automobile). Et c’est la société ITM Lemi, filiale intégrée du groupement, qui est chargée de la logistique de l’ensemble de ce pôle d’activité. Une activité internalisée, opérant depuis 2010, suite à la séparation des activités logistiques entre la partie alimentaire et non-alimentaire. « Nous sommes les héritiers de l’expertise logistique des Mousquetaires, acquise depuis plus de trente années », explique Thierry Roch, directeur général d’ITM Lemi. Pilotage des flux, approvisionnements, logistique et transport sont les quatre grands métiers de l’entreprise. Pour cela, la société s’appuie sur quatre bases logistiques en France : deux en Eure-et-Loir, les sites Garancières 1 et 2, ainsi que deux autres à Anais (16) et Albon (26), qui alimentent aujourd’hui environ 650 points de vente en France, avec des flux atteignant près de 30 millions de colis livrés par an. Ce réseau est également complété par un entrepôt situé en Chine, à Shanghai, permettant à l’entreprise de mieux maitriser ses flux d’importation venus d'Asie.
Mission intégration
Mais cette organisation fait face, depuis l’année dernière, à un nouveau défi : l’intégration de l’activité des 160 magasins Bricorama en France, suite au rachat de l’enseigne par le groupement Les Mousquetaires en janvier 2018, soit 30 % de chiffre d’affaires supplémentaires. « C’est une chantier qui nous occupe depuis un an sur la partie conception, et désormais au niveau opérationnel. Il s'agit d'un déploiement progressif, par palier, qui a pour objectif d’accueillir l’ensemble des points de vente d’ici la mi-septembre 2019. Nous en avons déjà intégrés 25 aujourd’hui sur les 166 présents sur le territoire. Bricorama possède deux sites logistiques gérés par des prestataires, dont nous sommes en train de transférer et d’intégrer l’activité », résume Thierry Roch. Pour cela, l’entreprise a lancé un grand projet d’agrandissement de ses moyens, aussi bien fonciers, avec une extension prévue pour Garancières 2), qu’humains, avec des recrutements prévus dans les années à venir. « Nous étions déjà en pleine réflexion sur ces questions avant. Bricomarché connaît une forte croissance, et se positionne comme la première enseigne indépendante dans le domaine des équipements de la maison. Mais l’ajout de Bricorama a accéléré les choses », précise Thierry Roch. Et pour absorber cette montée d’activité, ITM Lemi s’appuie en partie sur une installation automatisée et robotisée, qui a été mise en place dans son bâtiment de Garancières I.
Un système automatisé pour les petits conditionnements
Au sein de ce site ouvert en 1986 et présentant une surface totale de stockage de 62 000 m², l’entreprise a fait le choix, en 2016, d’automatiser la logistique des petits conditionnements (vis, outillage, prises, etc.) avec plusieurs objectifs : une optimisation de la productivité, une amélioration de la qualité de prestation pour les points de vente, une meilleure gestion de stock et un confort amélioré pour les collaborateurs dans leur travail. L’ensemble du système a été mis en place par le constructeur autrichien TGW, à la suite d’un appel d’offres auprès d’une demi-douzaine de sociétés spécialisées qui aura duré plus d’un an. Le résultat ? Une installation de 5 000 m² qui permet de traiter 8 000 références, soit la moitié des produits permanents proposés en magasin, et 40 % des flux de colis. Sur sept allées de huit mètres de hauteur, sont stockés entre 60 000 et 70 000 bacs, en rangement dit "chaotique" (c’est à dire qu’un même produit est éclaté à plusieurs endroits dans le stockage pour éviter toute rupture en cas de problème technique dans une allée). Ces bacs présentent deux formats différents selon le dimensionnement des produits stockés. Ces bacs présentent deux tailles différents selon le dimensionnement des produits stockés. La plupart sont en plastique mais certains se trouvent dans des emballages cartons. « Plusieurs de nos fournisseurs acceptent de se prêter au jeu et de mettre leurs produits directement dans des conditionnements pouvant être acceptés par la machine. Certains les intègrent directement dans nos bacs plastiques que nous leur fournissons. D’autres, si le produit le permet, nous proposent des cartons adaptés qui sont directement intégrés au système. Cela représente 50 % des produits aujourd’hui. Le reste est mis en bac manuellement sur le site par nos opérateurs, en réception », détaille Stéphane Renoux, directeur des opérations.
À l’entrée du système, chaque bac ou carton est intégré de deux manières différentes : soit par la machine de manière automatisée avec un système de préhenseur pour les palettes déjà préparées par les fournisseurs, soit en manuel par les opérateurs pour les produits mis en bac sur site. Chaque contenant est ensuite contrôlé automatiquement afin de vérifier son poids ou sa hauteur, puis est placé en stockage via un système de convoyage et d'ascenseur. D’un bout à l’autre de la chaîne automatisée, c’est la vitesse de déplacement qui surprend, avec une moyenne de plus de quatre mètres par seconde. « Nous avons fait un travail de réglage très fin pour atteindre un tel débit », explique Stéphane Renoux
Une préparation optimisée
La préparation des commandes des magasins s’effectue sur dix postes goods-to-man dont la conception ergonomique a été réalisée aux côtés des équipes, afin d’améliorer grandement la qualité de vie, avec un soin apporté à la hauteur du poste de travail, au positionnement de l’écran, etc. Jusqu’à quatre commandes peuvent être préparées en parallèle par un opérateur, qui va placer les produits à destination des magasins dans des emballages carton. Chaque carton préparé est dédié spécifiquement à une typologie de produit. « L’objectif de ce tri à la préparation est de faciliter la mise en rayon dès la réception dans les points de vente », explique Tony Nunes, directeur d’exploitation logistique chez ITM Lemi. Le process est simple : un bac venu du stockage vient jusqu’à lui et l’écran lui indique la quantité à prélever et le carton dans lequel déposer les produits demandés. « C’est l’opérateur qui tire le flux, selon son rythme », précise-t-il. Cette organisation permet également de faciliter la gestion des stocks, avec des contrôles réguliers du nombre de produits restants dans un bac ou des vérifications de la présence des bonnes références, pour éviter toute erreur ou rupture. Si le poids des cartons préparés est contrôlé par la machine pour éviter qu’ils soient trop lourd, c’est l’opérateur qui décide lui-même à quel moment le carton à destination du magasin est considéré comme idéalement rempli. « Se baser sur l’expérience des équipes est beaucoup plus productif et efficace que de s’appuyer sur des valeurs théoriques », estime Tony Nunes.
Après quoi ces cartons complets sont convoyés vers la zone de préparation de palettes ou de demi-palettes selon les besoins. Après avoir été fermés, les cartons sont classés automatiquement par ordre de poids par le système, afin de pouvoir mettre les plus lourds en bas. Un système de palettisation robotisé s’occupe ensuite de la construction de la palette puis de son filmage. En sortie, un opérateur transfère ensuite ces palettes complètes jusqu’à la zone d’expédition. Là-bas, ces produits petits formats rejoignent le reste des flux traités sur le site, pour leur part difficilement automatisables : lourds (sacs de ciment), avec des formats difficiles (brouettes, portes en bois) et des particularités (produits parfois dangereux). Un ensemble de références qui représente 60 % des colis traités par ITM Lemi avec de la préparation classique, avec l’aide de terminaux ou de systèmes vocaux. Dernier challenge : la préparation des remorques à l’expédition vers un ou plusieurs points de vente, livrés hebdomadairement. Entre des formats très hétérogènes, un travail sur la répartition du poids et une organisation logistique qui impose un chargement des produits par l’arrière mais un déchargement en point de vente sur le côté, les chargeurs ont fort à faire pour permettre un transport optimisé.
Aujourd’hui, à l’inverse de son jumeau Garancières 2, situé à quelques centaines de mètres, le site de Garancières 1 ne pourra pas connaître d'extensions, n’ayant plus de réserve foncière disponible. Mais les projets continuent cependant sur ce bâtiment historique. En effet, si le système automatisé n’est pas encore arrivé à saturation aujourd’hui, ITM Lemi envisage d’ores et déjà de futurs développements : un espace est ainsi réservé pour une allée de stockage supplémentaire, et un onzième poste goods-to-man pourrait facilement être créé, si besoin est, dans les années à venir.
L'installation automatisée de ITM Lemi en images :
Le site de Garancières 1 en chiffres :
■ 62 000 m² de stockage
■ 650 points de vente livrés par semaine
■ 200 collaborateurs en CDI
■ 600 petits colis traités par heure
■ 4 mètres par seconde en vitesse de déplacement
■ 8 000 références traitées par l'instlalation automatisée
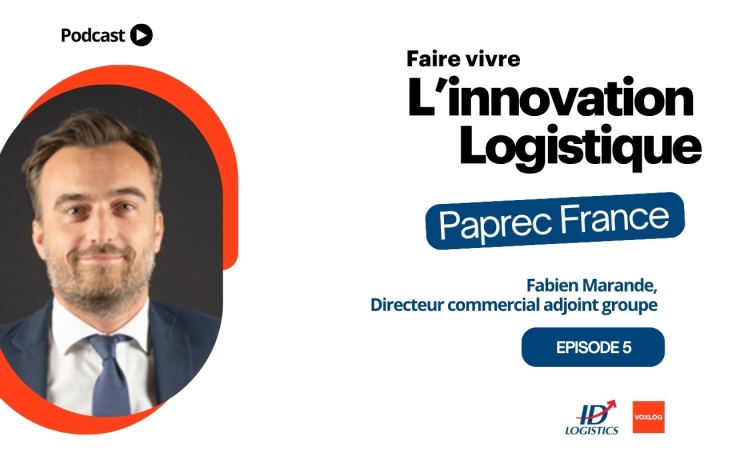