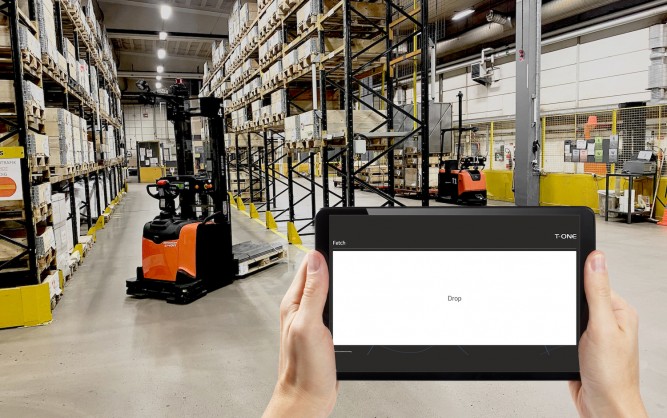
©
Toyota MH
Entrepôts
Comment installer des AGV et AMR dans son organisation logistique ?
Analyse des flux, cartographie des sites, connexion avec les systèmes d’information : si la mise en place de solutions AGV et AMR au sein de sa supply chain reste plus simple et rapide qu’un système automatisé fixe, elle nécessite tout de même l’expertise de spécialistes pour être menée à bien.
Comme pour toute installation automatisée au sein d’une organisation supply chain, la mise en place d’AGV ou AMR nécessite des étapes d’études et d’échanges en amont afin de développer une solution idéalement dimensionnée. En ce sens, la première étape est celle de la définition du système à installer. Face à ces questions, les constructeurs se font analystes des flux afin d’identifier les pistes qui auraient du sens : « Il y a beaucoup de critères à prendre en compte. Tout d’abord un aspect technique, que les clients ont de plus en plus en tête, car l’automatisation requiert des modifications au sein de leur entrepôt. Il peut y avoir une standardisation à mener, notamment sur les types de charges et leur homogénéisation, afin de faciliter la mise en place de process optimisés. De plus, il n’est pas toujours possible d’automatiser tous types de support de charges, d’où l’importance d’échanger avec le client pour définir le périmètre de l’automatisation », détaille Éric Deffontaines, responsable d’activité AGV chez Jungheinrich. Le constructeur analyse ainsi les données de base du projet, les charges à transporter, et les flux à traiter : « Il faut que le client définisse exactement ce dont il a besoin en termes de dimensions et spécificités des process. Ce sont ces données de base qui nous permettent de proposer une enveloppe, pour préciser combien de machines seront nécessaires, et pour quel montant. Still accompagne le client dans le calcul de son ROI par rapport à sa capacité d’investissement et le nombre de personnes qu’il mettrait en face pour faire le même travail », évoque Bruno Chambraud, responsable du département intralogistique chez Still France.
Et les éléments à préciser en amont sont nombreux pour bien cadrer le projet : « Il faut étudier les typologies des charges, leurs capacités de préhension, leurs dimensions, leur poids, leurs centres de gravité. Après quoi, nous regardons la spécificité des flux : quoi transporter, où, et à quelle fréquence ? Les performances ne sont pas toujours les mêmes entre les solutions proposées. Certaines peuvent être plus onéreuses mais plus rapides et efficaces. Ensuite, il faut étudier l’intelligence à mettre derrière : est-ce une intégration avec un ERP d’usine ou même avec un WMS, ou un système simple avec des boucles fermées ? Cela dépend là encore du niveau d’automatisation recherché », détaille Jérémy Cimelli, ingénieur robotique du département AGV chez Aprolis.
Des contraintes pensées pour rester limitées sur le site
Si le but est donc de changer au minimum l’installation des clients, les experts du sujet soulignent la nécessité d’adapter l’existant à l’arrivée de l’automatisation. « Il faut absolument avoir une volonté de conduite du changement, car la friction entre les parties prenantes peut entrainer de vrais retards », regrette Jérémy Cimelli. Celui-ci souligne le travail à réaliser pour repenser certains flux, principalement sur des sites de production intégrant déjà des systèmes de « trains » pour l’approvisionnement de certaines zones. « Il faut réorganiser les déplacements, et éviter par exemple les doubles sens de circulation où l’on ne peut pas se croiser », note Jérémy Cimelli. Des contraintes de sécurité afin de créer l’espace nécessaire pour que les machines se meuvent sans problème au sein de l’entrepôt. À ce titre, certains soulignent alors le choix à faire entre les AGV, aux routes bien tracées, et les AMR qui peuvent évoluer plus librement, mais avec des contraintes plus fortes. « Avec les AMR, des règles doivent être définies : rouler à une certaine distance des obstacles quand il faut les contourner, éviter certains éléments fixes, etc. A contrario, quand vous définissez les routes d’un AGV, vous allez prendre le soin d’éviter les obstacles et n’aurez pas à mettre en place de règles spécifiques. Un AMR offre donc des capacités de déploiements plus rapides sur des projets simples, mais potentiellement plus longues sur les projets compliqués », avertit Jérémy Cimelli. Là encore, c’est la définition de l’organisation interne du site qui pourra faire pencher la balance vers une technologie ou une autre. À noter également la nécessité d’anticiper les emplacements des zones de recharges des AGV et AMR, vers lesquelles les machines vont automatiquement se déplacer lorsqu’elles atteignent un certain niveau de batterie.
L'indispensable connexion aux systèmes d'information
Mais intégrer de l’automatisation dans son entrepôt, c’est aussi mettre en place une communication entre les robots autonomes et des systèmes d’information, ERP ou WMS, qui viendront leur donner leurs missions. Constructeurs et intégrateurs insistent donc sur l’importance d’intégrer les équipes informatiques du client le plus en amont possible, pour bien identifier les besoins et attendus en termes de connexion, de couverture Wi-fi dans l’entrepôt et de cybersécurité. Les AGV ont besoin de communiquer à distance avec le système d’information du client, ce qui peut nécessiter des validations en interne. « Il faut que les équipes IT soient présentes au démarrage, car l’informatique est la clé de voute de tels projets. Il ne faut absolument pas réaliser trop tard que l’on n’avait pas prévu ces aspects de communication », confirme Yannick Antoine chez Toyota Material Handling France. Là encore, les caractéristiques du projet vont faire varier les exigences : « Si vous restez sur des boucles fermées très simples, la connexion avec les systèmes d’information existants ne sera pas un problème. Mais dès lors que vous avez des ordres venus directement de l’ERP ou du WMS en temps réel, cela peut prendre plus de temps. D’autant que les solutions de certains grands acteurs des ERP sont parfois difficiles à intégrer car elles n’ont pas été pensées pour un process AGV », explique Jérémy Cimelli.
Le rôle du logiciel de pilotage des flottes automatisées est crucial pour le bon fonctionnement des solutions AGV et AMR. Chez Alstef Group, une nouvelle suite logicielle, intitulée Opal, « rassemble sous une même solution notre capacité à assurer aussi bien la gestion de flotte AGV que la gestion de stock, la préparation de commandes et le séquençage », note Sébastien Dumon, chef de produit solutions intralogistiques chez Alstef Group. Elle se décline en différents modules selon les process automatisés, qui vont s’interfacer avec les ERP et WMS : « La difficulté d’intégration va dépendre surtout des interactions. Parfois, elles sont très réduites, avec seulement des déplacements réguliers sur des kilomètres et sans contacts humains. Mais certaines machines peuvent être en lien direct avec les opérateurs, ce qui nécessite plus de travail selon les spécificités du site », explique Sébastien Dumon. Du côté de Toyota Material Handling, les AGV s’appuient sur une partie software baptisée T-One : « Nous allons du simple système de gestion d’activité des chariots et du trafic, avec prise en compte des priorités, jusqu’à la réception des données venant d’un WMS avec des solutions préétablies qui touchent les métiers de la réception, du gerbage, de la préparation, ou de la mise en stock des produits finis. Tous ces modules sont déjà installés dans T-One et fonctionnent comme une grande boite de Lego, ce qui permet une mise en œuvre rapide », détaille Yannick Antoine. « Nous avons beaucoup travaillé afin que le client puisse répondre à ses évolutions, en changeant du jour au lendemain les missions. Il faut une industrialisation des missions et des softwares, pour ne pas être sur du codage spécifique unité par unité, ou site par site ».
Un travail mené aussi du côté des éditeurs
Du côté des éditeurs, on accompagne ce mouvement vers l’automatisation. C’est le cas chez Acteos, comme l’explique Jean-Michel Lefebvre, directeur grands comptes : « Dans notre suite logicielle, nous avons un WMS qui dispose d’un module de pilotage visant à optimiser l’ensemble des mouvements à réaliser, que ce soit une préparation B2B ou B2C, ou des palettes à déplacer. Dans le cadre de la mise en place d’un AGV ou AMR, on connecte ce module de pilotage avec le système automatisé, en allant plus ou moins loin selon les missions. Pour les boucles d’AGV, il vaut mieux laisser leur système piloter l’intégralité des mouvements. Mais dans le cas de déplacements autonomes dans l’entrepôt, il faut que le WMS se charge du pilotage, car il est le seul à même de gérer les priorités. Chez notre client Placoplatre, des AGV récupèrent les plaques de plâtre en sortie de fabrication, et les amènent vers le stockage. Dans ce cadre, c’est au WMS de dire à l’AGV où placer ces palettes, avec un pilotage en temps réel ».
Autre projet chez Acteos, dans le monde pharmaceutique : AstraZeneca, qui a étendu son site logistique à Dunkerque. « Certains AGV évoluent dans l’entrepôt de stockage et d’autres vont assurer les transits jusqu’au lieu de production, dans un sens (matières premières, matériaux de conditionnement) comme dans l’autre (produits finis vers le stockage). Ces mouvements sont pilotés par le WMS qui va, en fonction de caractéristiques des articles et des règles de gestion, faire passer l’AGV par une zone de filmage par exemple. C’est tout un ensemble de décisions qui sont ainsi prises par le logiciel de gestion d’entrepôt », note Jean-Michel Lefebvre. Avec toujours un point essentiel : la capacité du WMS à interagir en temps réel avec les systèmes automatisés. « L’efficacité de nos solutions est permise grâce à la connexion de notre logiciel de management des flottes de robots avec le WMS de nos clients », résume Jackson Zhang, vice-président de Geek+ Europe.
Focus
Pour les AMR, une cartographie menée en amont du déploiement
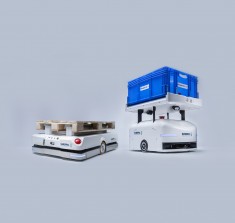
La cartographie de l’entrepôt logistique ou du site industriel est une étape indispensable en amont du déploiement des AMR. Une fois achevée et optimisée par un certain nombre de règles, celleci permet au système de pilotage des robots de les faire évoluer en toute sécurité. « Pour réaliser cette cartographie, nous prenons un AMR sur lequel nous branchons une manette, et nous le faisons évoluer dans l’entrepôt en contrôle manuel. Avec ses capteurs multiples (deux lidars horizontaux, deux radars verticaux ainsi que des gyroscopes, accéléromètre et odométrie), l’AMR découvre et mémorise les points de l’entrepôt, et réalise une carte grâce à la combinaison de toutes les informations », détaille Marc-Antoine Fernet, chef de produits robotique et nouvelles technologies chez Savoye. « La première étape de la mise en service consiste à cartographier le site. Cette opération est réalisée soit par le client final après une formation soit par un de nos distributeurs ou intégrateurs. On va ensuite élaborer les règles de circulation du robot mobile puis définir des positions (points de départ et d’arrivée) et des points d’accès dans l’entrepôt. Enfin, il s’agit de créer des missions, avec tout type de combinaisons possibles, et établir des fonctions logiques (si une zone est occupée, le robot va ailleurs ; si sa batterie est seulement à 10 %, il va aller se charger seul) », note Olivier Pommares, responsable commercial France chez Mobile Industrial Robots (Mir). La durée de ce processus dépend donc de la taille du site et de la surface à cartographier, mais aussi de la complexité d’intégration et des flux à automatiser : « Pour des actions de roulage et de transfert manuel, le paramétrage peut ne prendre que trois ou quatre jours. Mais si les parcours sont plus compliqués, avec des ascenseurs à emprunter ou une intégration avec le WMS pour des missions précises, les durées peuvent s’allonger. En moyenne, définir 50 positions sur un site de 500 m² pour une trentaine de missions nécessite autour d’une semaine », détaille Olivier Pommares. Quand cette opération de terrain est réalisée, le roboticien va ensuite affiner la carte, il nettoie tout ce qui n’a pas fonction à être pérenne dans l’espace de l’entrepôt et va définir des règles de circulation bien précises : les écarts à respecter par rapport aux murs et éléments fixes de l’entrepôt, l’évitement de certaines portes, etc. « Par exemple, si le champ de vision dans une zone donnée est réduit, on va automatiquement faire baisser la vitesse de l’AMR dans un espace donné. Lorsque la cartographie est achevée, tous les AMR peuvent l’utiliser pour se mouvoir de manière autonome », précise Marc-Antoine Fernet.
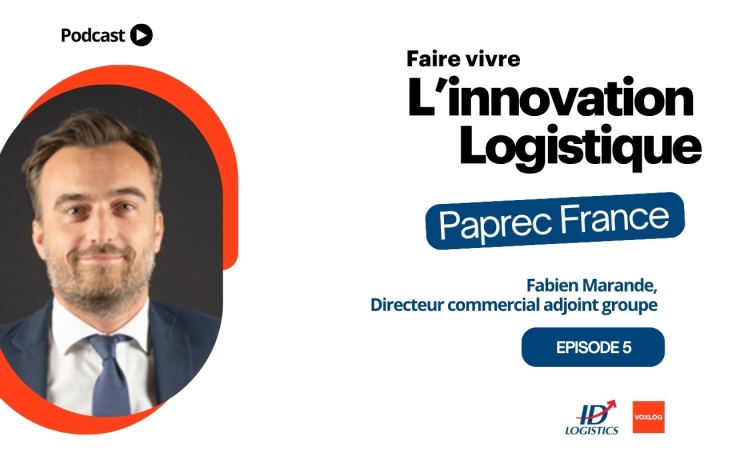