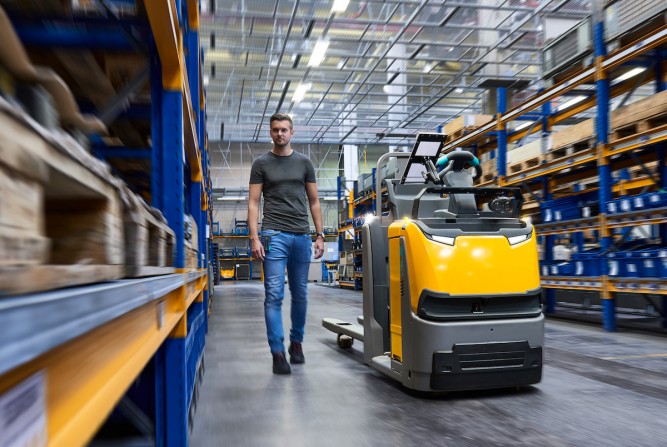
©
Jungheinrich
Entrepôts
Les véhicules logistiques embarquent de nouvelles composantes digitales
D’un modèle à l’autre, les constructeurs de véhicules dédiés à la logistique viennent ajouter de nouvelles composantes digitales à leurs catalogues. Qu’elles sécurisent les process en entrepôt ou apportent plus de productivité, celles-ci viennent offrir de l’intelligence au service des opérateurs et des managers. Retour sur quelques-unes de ces innovations discrètes.
« Aujourd’hui, un véhicule logistique n’est pas seulement un outil, mais potentiellement un levier de productivité global ». Voilà comment Jean-Jacques Boulet, responsable marketing chez le loueur et vendeur Aprolis, résume l’évolution des chariots, transpalettes et autres gerbeurs. Un basculement permis « par l’essor de l’électronique embarquée, d’autant que les technologies sont toujours plus présentes et que leur coût baisse ». Un avis partagé par Aurélia Doffenies, responsable marketing des services et formation commerciale chez le constructeur Fenwick : « Le monde de la supply chain évolue, avec des besoins client en perpétuelle mutation, ainsi qu’un environnement réglementaire toujours plus contraignant. Dans ce contexte, Fenwick doit s’adapter et apporter des solutions innovantes. L’accent est donc mis sur le développement de nouvelles solutions embarquées qui vont rendre le chariot intelligent et permettre au client d’améliorer la sécurité de ses opérations, qui n’est plus une option aujourd’hui, et par ricochet sa productivité ». De série ou en option, les composantes digitales sont ainsi toujours plus nombreuses au sein de ces véhicules, et en font des outils connectés.
Des véhicules plus sûrs
Du côté de la sécurité, les chariots se voient ajouter de nouvelles solutions depuis plusieurs années : gestion de la charge, assistance dans les virages pour éviter les basculements (le système Curve Speed Control chez Still), caméra de recul ou encore systèmes de contrôle dynamique du mât pour compenser les oscillations (tels que le BlueSpot de Fenwick). Chez Still, ces systèmes sont gérés directement depuis un écran LCD couleur qui permet aux opérateurs de contrôler ces réglages. Mais les chariots peuvent aussi se baser sur le lieu où ils circulent. Des solutions de gestion par zone se sont ainsi développées, permettant d’imposer aux véhicules des actions de sécurité précises dans certains endroits de l’entrepôt. Chez Jungheinrich, « des régulations automatisées de la vitesse ou des notifications particulières pour les opérateurs pendant la conduite peuvent être mises en oeuvre automatiquement », comme l’explique Elena Perennes-Lonchamp, responsable nationale des ventes SAV.
Un focus sécurité que Fenwick a également décidé de mettre au coeur de son offre avec sa solution Safety Guard. Dévoilée il y a six mois, elle propose un système d’avertissement de proximité et de prévention des collisions, pour réduire les risques d’accidents aussi bien entre chariots qu’au niveau des personnels ou de l’infrastructure en entrepôt. Celui-ci permet de paramétrer des réductions automatiques de vitesse dans certaines zones, programmer des actions sur l’infrastructure (actionner l’ouverture d’une porte au passage d’un chariot par exemple) ou avertir le cariste de l’approche d’un piéton ou autre véhicule par le biais d’alertes visuelles et sonores. Un boitier installé sur les chariots permet l’utilisation de cette solution, fonctionnant en ultra wide band 4 GHz, « une méthode de communication peu utilisée en entrepôt donc très stable, qui ne va pas perturber les ondes des clients équipés de wi-fi par exemple, et qui permet d’être très précis, à 10 centimètres près », explique Aurélia Doffenies. Les opérateurs à pied peuvent être équipés d’un badge qui communique avec les chariots pour assurer la détection piétonne, tandis que des tags sont placés au niveau de l’infrastructure pour gérer la réduction de vitesse dans certaines zones à risque. « C’est une offre très modulaire. Parmi les clients qui nous interrogent pour ce type de prestations, 80 % sont intéressés par les solutions de réduction de vitesse en zone ou pour du contrôle d’infrastructure. Seuls 20 % nous demandent de la détection piéton. Cela concerne principalement des clients ayant déjà des solutions de prévention des risques très abouties et qui souhaitent aller plus loin. Aujourd’hui, nous visons principalement le monde industriel, comme le secteur de la boisson qui fait face à des problématiques de forte cohabitation entre piétons et chariots en entrepôt », détaille Aurélia Doffenies.
Automatiser une partie des process
Autre avantage de ces composants digitaux intégrés dans les chariots, la possibilité d’ajouter des éléments d’automatisation au sein des activités des opérateurs. Chez Jungheinrich, cette possibilité se nomme Easypilot. Dévoilée l’année dernière et capable d’équiper, par exemple, les préparateurs de commandes horizontaux, cette technologie permet au chariot de suivre l’opérateur pendant le picking pour lui éviter des déplacements inutiles. La solution propose plusieurs vitesses et offre la possibilité de choisir la position à laquelle s’arrête le véhicule par rapport à son conducteur, le tout avec des sécurisations par radar pour éviter les chocs. Un système fonctionnant grâce à une télécommande équipée d’un capteur en technologie ultra wide-band. « Dès que le préparateur dépasse les fourches, le chariot avance seul pour rester à son niveau. Son usage devient plus simple, soulageant les équipes et leur apportant plus de confort. On réduit le temps de conduite pour augmenter le temps de picking. C’est une solution en évolution croissante », explique Anthony Soubrier, chef produit rétractables et préparateurs de commandes chez Jungheinrich France. L’entreprise estime que le gain en productivité peut être de l’ordre de 30 %. Chez UniCarriers, on retrouve également ce type de système d’assistance à la conduite, avec de la programmation de hauteurs pour prélever plus facilement et avec plus de sécurité les éléments en entrepôt. Une solution que le constructeur a voulu simple et sécurisante. « Plutôt que d’avoir à appuyer sur un bouton pour lever automatiquement ses palles, l’opérateur va les monter manuellement, d’un palier préenregistré à l’autre, sans quitter sa charge des yeux le conduisant donc à être plus proactif. La digitalisation nécessite de trouver un juste équilibre entre sécurité et productivité, et c’est ce que nous souhaitons apporter à nos clients », explique Frédérik Bodelot. Des méthodes que l’on retrouve également chez Still avec la solution Optisafe, qui là encore à pour objectif d’offrir une vitesse optimale aux opérations sans sacrifier la sécurité. Des transpondeurs RFID ou des étiquettes codes-barres peuvent ainsi être installés dans l’entrepôt afin d’aider à la conduite le long des rayonnages en tenant compte automatiquement de conditions spécifiques pour chaque allée. Le système Optispeed 4.0 sécurise lui le processus dans les allées étroites avec de la direction semi-automatique qui place le chariot et la fourche dans une position optimale par rapport aux infrastructures de l’entrepôt afin d’éviter les manoeuvres. Et cette automatisation discrète des process peut faire de ces véhicules de véritables chariots connectés comme le décrit Romain Lemaire, responsable produits de magasinage chez Aprolis : « Un chariot tridirectionnel utilisé en allées étroites a pour mission d’être le plus actif possible. Il faut donc que son utilisateur ait le plus d’informations en temps réel pour suivre les besoins de la production. On voit donc se développer des systèmes connectant le WMS et le chariot. Le logiciel va recevoir des informations de commandes et celles-ci peuvent être retranscrites et transmises au véhicule. Ce dernier va comprendre où se situe le produit à prélever et aller directement jusqu'à l'emplacement, s'il se trouve dans la bonne allée. Il peut ainsi choisir la meilleure courbe de conduite, de levage et optimiser son déplacement selon des règles de productivité et de sécurité, sans intervention de l’opérateur ». Des systèmes qui peuvent être mis en place facilement grâce à l’installation de puces RFID dans l’entrepôt qui sont lues par le véhicule. « Aujourd’hui, tous les logisticiens sont équipés de WMS. Il est donc logique que les constructeurs cherchent à adapter leurs chariots pour créer des synergies avec les systèmes des clients. Ce sont des installations que l’on retrouve en logistique industrielle principalement, mais également dans des entreprises qui ont des besoins de réactivité ».
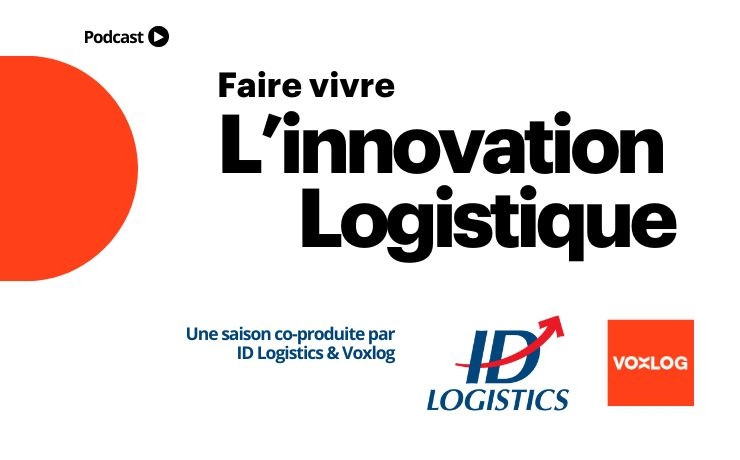