Chargeurs
E. Leclerc inaugure une solution logistique automatisée à la Socamaine
[+Vidéo] La Socamaine, centrale d'approvisionnement régionale du mouvement E. Leclerc basée près du Mans (72), s'est équipée d'une nouvelle solution logistique entièrement automatisée dédiée à son activité pour les produits secs. Un important système aux cadences industrielles qui lui permet d'ores et déjà de préparer 62 500 colis par jour.
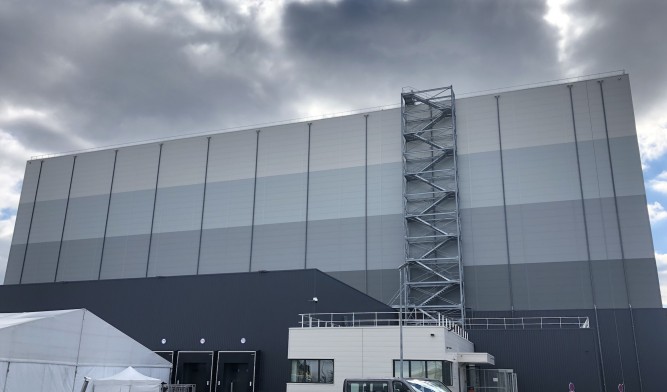
©
Voxlog | Le bâtiment Socamaine 4
Le grand mouvement de l'automatisation continue au sein des centrales d'approvisionnement régionales du groupement E. Leclerc. Après des projets menés ailleurs en France (Scapest, Scapnor...), c’était au tour de la Socamaine d’inaugurer, le 20 mars 2019, un nouvel outil logistique automatisé sur son site de Champagné, dans la Sarthe à proximité du Mans. Créée en 1976, troisième centrale de France, la Socamaine réalise un chiffre d’affaires annuel de 1,3 milliard d’euros et s’occupe de la distribution pour 39 magasins et 52 drives dans neuf départements. Un nombre de points de vente qui a doublé entre 2007 et 2014. Faisant également face à une augmentation de ses volumes de plus de 30 % sur la même période, la Socamaine devait donc répondre de manière efficace à l’évolution de ses besoins en repensant son organisation logistique. La centrale décide alors de se tourner vers la robotique et l’automatisation. Une nécessité selon Michel-Édouard Leclerc, président du mouvement E. Leclerc : « Nous devons augmenter notre maitrise de la logistique et de l’approvisionnement rapide. Un outil comme celui de la Socamaine nous permettra de livrer aussi bien des drives, des points relais Leclerc, des particuliers à domiciles que des hypermarchés, parce que la robotique et l’intelligence introduites en amont nous permettent de faire tout cela à moindre coût. De plus, la robotisation conduit à éviter les tâches pénibles et répétitives. C’est en s’équipant de moyens logistiques et techniques de ce type que nous pourrons lutter demain contre Amazon ».
Un projet d'automatisation progressive
Ce projet de fond est lancé dès 2011, avec un premier tour d’Europe des solutions automatisée effectué par les équipes de la Socamaine. Rapidement, la coopérative régionale s'associe à la société d'ingénierie logistique SDZ Processréa pour piloter avec eux ctte initiative, comme l’explique son directeur général, François Mondou : « Nous sommes intervenus dès 2012 dans le cadre d’une réflexion sur l’évolution du site face à sa croissance. Nous avons été en charge du design global du process et du système informatique de la solution. Le projet présentait plusieurs spécificités. Tout d’abord, la décision de la Socamaine de rester sur son site et d’utiliser son bâtiment existant Socamaine 3 [créé en 2007] pour l’installation de la solution automatisée, afin de capitaliser sur ses actifs. L’idée a donc très vite consisté à se doter d’un magasin de stockage en grande hauteur, avec la capacité de pouvoir l’étendre, et de le relier au bâtiment existant Socamaine 3 via une galerie en hauteur ». Un projet d’automatisation fort vers lequel la Socamaine a souhaité opérer une transition en douceur, en intégrant au système seulement 50 % des volumes de son activité PGC (produits de grande consommation). « Pour la Socamaine, il s’agissait d’être progressif dans l’automatisation. Ce sont aujourd'hui les produits les plus lourds et les plus pénibles pour les collaborateurs qui ont été automatisés, soit 7 200 des 11 000 références disponibles. Le reste continue à être géré sur les autres sites de la Socamaine de manière traditionnelle, l’ensemble des commandes étant ensuite regroupé de manière indifférenciée en expédition. Mais l’objectif consiste à poursuivre cette automatisation dans les années à venir pour intégrer le reste de l’activité PGC », explique François Mondou.
Une solution flexible
Après un grand appel d’offres lancé auprès de sept grands constructeurs européens, la société néerlandaise Vanderlande a été sélectionnée. « Nous avons montré beaucoup de flexibilité dans notre approche, notamment au niveau de l’implantation avec l’utilisation de deux sites, ce qui a nécessité un travail rapproché avec le génie civil et l’entreprise GSE, principalement pour la passerelle entre les deux bâtiments. Cependant, l’aspect très modulaire de notre système nous a permis de nous adapter aux besoins de la Socamaine. Aucun travaux de rénovation n’ont ainsi eu à être réalisés dans l’ancien bâtiment », explique Pierre Goemaere, directeur général de Vanderlande France. « Notre flexibilité était également importante du point de vue de la maintenance. Nous sommes dans une optique de formation du client. Nous serons présents dans les six premiers mois pour offrir une montée de puissance, puis nous laisserons la main aux équipes de la Socamaine ». Des arguments qui ont su convaincre d’autres centrales régionales de E. Leclerc : Vanderlande est désormais en train de travailler sur un grand projet d’automatisation pour le compte de la Scadif, située dans le sud de l’Île-de-France (entre Réau et Savigny-le-Temple en Seine-et-Marne), qui devrait rentrer en activité à l’horizon 2022. Objectif, prendre en charge 85 % des volumes pour les produits de grande consommation.
Au total, 30 mois de travaux auront été nécessaires pour la mise en place du système de la Socamaine dont la construction a été finalisée en avril 2018. En montée en charge depuis désormais plusieurs mois, le transfert de propriété vers la plateforme régionale du nouveau système sera officialisé à la fin du mois de mars 2019. Avec cet équipement, la Socamaine a anticipé les besoins de ses supermarchés et de ses drives pour les dix années à venir.
Un système entièrement automatisé
C’est dans le nouveau bâtiment de la Socamaine 4 que débute le nouveau process automatisé. Un entrepôt de très grande hauteur, 42 mètres de haut, offrant une capacité de 6 000 m² au sol. Dans celui-ci se trouve tout d’abord l’espace de réception, où près de 1 500 palettes seront reçues quotidiennement par la centrale. Ces palettes sont ensuite intégrées au système automatisé par trois lignes d’injection puis amenées par un système de convoyage jusqu’à la zone de stockage grande hauteur. Équipée de six transstockeurs, celle-ci affiche une capacité de 35 000 emplacements en double profondeur. Quand elles font l’objet d’une commande, les palettes sortent alors du stock et sont amenées jusqu’au bâtiment voisin Socamaine 3. Ce transfert est réalisé grâce à une galerie couverte en hauteur, passant à plusieurs mètres au dessus du système routier de la Socamaine, qui permet d’apporter les palettes ou de les faire revenir vers le stock grâce à deux lignes de convoyage parallèles. 62 mètres séparent les deux bâtiments, suite à des contraintes réglementaires (l’espace entre eux devait être 1,5 fois plus grand que la taille du bâtiment grande hauteur en cas d’incendie). Mais cette contrainte est également bénéfique comme le souligne François Mondou : « Cette galerie peut permettre d’absorber un partie des flux en cas de pic d’activité par exemple. La contrainte technique est donc devenue un avantage ».
Au sein du bâtiment Socamaine 3, les palettes arrivent dans une zone de dépalettisation. Après un défilmage effectué par un collaborateur de la Socamaine, elles sont ensuite amenées jusqu’à trois puits de dépalettisation où deux opérateurs vont alors s’occuper de prélever les colis nécessaires aux commandes pour les mettre sur les plateaux individuels. Un processus manuel, avec une capacité de traitement de 3 200 colis par heure, qui a fait l’objet de beaucoup d’attention afin de lutter efficacement contre les TMS. Placés sur des stations ergonomiques, les collaborateurs n’ont ainsi plus à porter les produits : arrivant directement au niveau de leur poste, les colis doivent uniquement être poussés et glissés jusqu’aux plateaux. « Nous avons fait venir des opérateurs de la Socamaine pour travailler avec des ergonomes. Nous étions réellement dans une démarche d’échange et de partenariat au service du client », détaille Olivier Labous, business development manager food chez Vanderlande.
Une préparation industrialisée
Une fois placés sur les plateaux, les produits sont installés dans un stockage temporaire, composé de 10 rangées et 100 navettes shuttle. Celui-ci est situé au sein d’une cellule dédiée de la Socamaine 3, auparavant utilisée pour des process logistique standard, et dont seulement 9 000 m² sur 16 000 m² sont utilisées aujourd’hui, offrant donc des capacités d’agrandissement du stockage shuttle si nécessaire, pour une intégration d’une plus large partie de l’activité PGC. « C’est l’intelligence de ce projet que d’avoir su utiliser les bâtiments existants en se laissant de l’espace pour les projets futurs », résume François Mondou. Après quoi, la préparation des palettes se fait grâce à cinq modules de palettisation. Pouvant traiter jusqu’à 62 500 colis quotidiennement sur un rythme de 21 heures de production (six jours sur sept), ceux-ci sont chacun composés de deux bras robotisés : le premier va déplacer le produit par poussée jusqu’à proximité de la palette, tandis que le second va se saisir du colis grâce à un système de préhension pour le placer à l’endroit nécessaire. Au-dessus d’eux, des caméras vérifient que chaque colis pris est le bon, est bien placé, au bon endroit. Les palettes sont composées grâce à des systèmes algorithmiques qui suivent différentes règles de stabilité (produits lourds en bas de palette) et de productivité (palettes par famille de produits afin de simplifier leur éclatement dans les rayons des magasins ensuite). Enfin, après avoir été filmées et étiquetées, les palettes hétérogènes constituées sont emmenées en zone d'expédition aux côtés de celles de l'activité logistique traditionnelle.
Si on y ajoute le montant de la réalisation d'un nouveau bâtiment pour l'activité des produits frais (finalisé parallèlement et nommé Socamaine 5), l'ensemble des investissements réalisés par la Socamaine s'élève à un total de 66 millions d'euros. La centrale se montre donc pour l'instant patiente et discrète sur la poursuite de sa transformation logistique. S'il n'est pas fait mention de phase 1 ou 2, une chose est sûre : la grande révolution de l'automatisation n'est pas encore terminée à la Socamaine.
L'installation de la Socamaine en images :
La solution automatiséede la Socamaine en chiffres :
■ Un nouveau bâtiment de 42 m de haut et 6 000 m² ;
■ Capacité de stockage 35 000 palettes et 46 200 plateaux ;
■ 6 transstockeurs pour le stockage grande hauteur ;
■ 100 navettes pour le stockage temporaire ;
■ 5 robots de palettisation pour une capacité de 62 500 colis par jour.
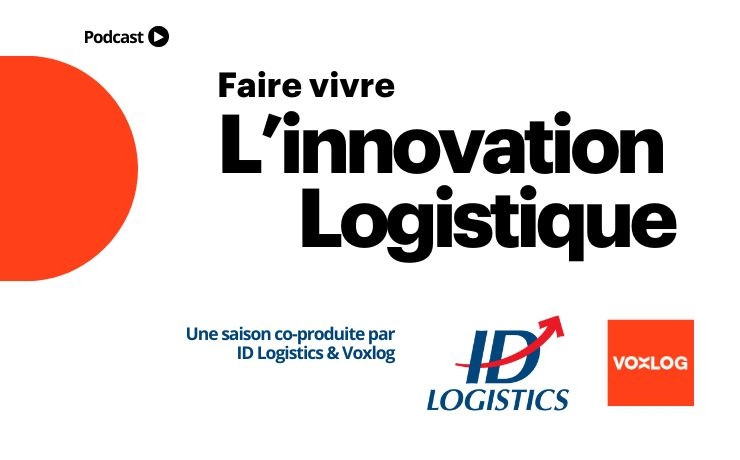