Innovation
2. Mélanger réel et virtuel
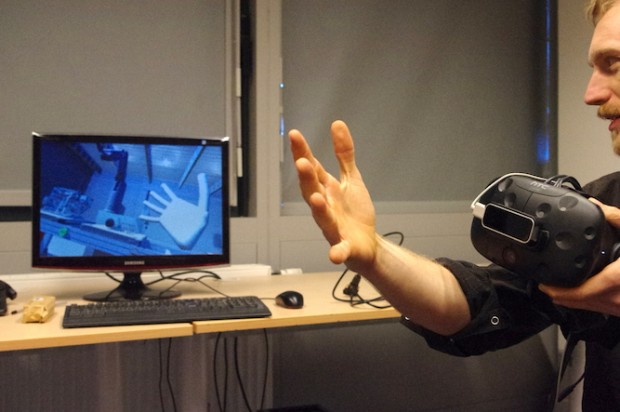
Hausse de la fiabilité et de la compétitivité, pénibilité amoindrie dans les tâches des opérateurs… Incorporer la réalité augmentée dans les chaînes de montage devient un enjeu majeur pour les industriels. Au sein de FactoryLab, start-up et grands groupes testent des outils numériques pour arriver à un but précis : le zéro défaut.
En matière de réalité augmentée, le moteur d’avions LEAP de Safran destiné à équiper les avions monocouloirs de nouvelle génération est déjà un cas d’école. Dans l’usine de Villaroche de sa filiale, Safran Aircraft Engines, les opérateurs ne travaillent plus seuls. Des écrans tactiles et des rétroprojecteurs les soutiennent dans le montage des pièces. Un écrou qui n’est pas assez serré ? Un outil numérique conçu pour mesurer la force de serrage s’en charge. Un doute sur l’emplacement d’une pièce ? Pas d’inquiétude, un dispositif de réalité augmentée projective affiche sur le LEAP l’endroit précis où la poser. Bref, chez Safran, si l’on superpose le virtuel au réel sur les chaînes de montage, c’est parce qu’on porte haut et fort le message de la qualité. Il s’agit d’un moteur d’avion, après tout. Et tout doit se faire au millimètre près. « Aujourd’hui, les opérateurs sont amenés à travailler sur des équipements complexes et doivent s’adapter à la diversité des chaînes de production qui évoluent de plus en plus vite et avec beaucoup de flexibilité, analyse Sylvie Naudet, chef de projet Agora, programme au sein de FactoryLab qui a pour objectif de démontrer l’intérêt de la réalité augmentée. En apportant cette information sur leur poste de travail, le but est d’améliorer les performances et réduire le taux d’erreur. »
Pour atteindre ce degré de précision, le groupe d’aéronautique, de défense et Sécurité fait confiance à une PME : Diota. Cette start-up est le petit chouchou de Safran. L’entente entre les deux est telle que le géant français a intégré son capital en septembre dernier. La raison : son logiciel développé par la PME avec le CEA List. Contrairement aux systèmes qui utilisent des petits marqueurs optiques à placer sur les équipements et qui prennent du temps en termes de déploiement, la solution de Diota fonctionne sans marqueur. Autrement dit, elle identifie immédiatement tout objet dont le modèle 3D figure dans sa bibliothèque. Un véritable gain de temps pour l’opérateur. Et, au final, un gain de compétitivité pour Safran.
Soulager la pénibilité
Il y a un autre intérêt à mélanger le virtuel et le réel, celui de la formation. De ce côté, sur la plateforme FactoryLab, un projet vaut le détour. Un casque de réalité virtuelle Oculus Rift sur le nez, l’employé, pistolet à peinture vide dans la main, peut s’entraîner à peindre une porte de voiture, par exemple. Ici, pas de gâchis de peinture, puisque tout est virtuel. Juste un employé qui bouge dans le vide mais qui travaille de façon « ludique » à ajuster son geste. « Par nos moyens de simulation, nous pouvons prendre une maquette 3D qui représente le poste de travail, le process mis en œuvre et demander à un opérateur de jouer virtuellement son scénario, explique Laurent Chodorge, chef du Laboratoire Simulation interactive du CEA List. On suit ses mouvements, on fait de la motion capture, du tracking de ses gestes pour suivre en temps réel ses actions pour aider au diagnostic du poste de travail en termes de pénibilité et commencer à proposer dès la phase numérique, des moyens de l’assister, de soulager la pénibilité et d’optimiser les process. »
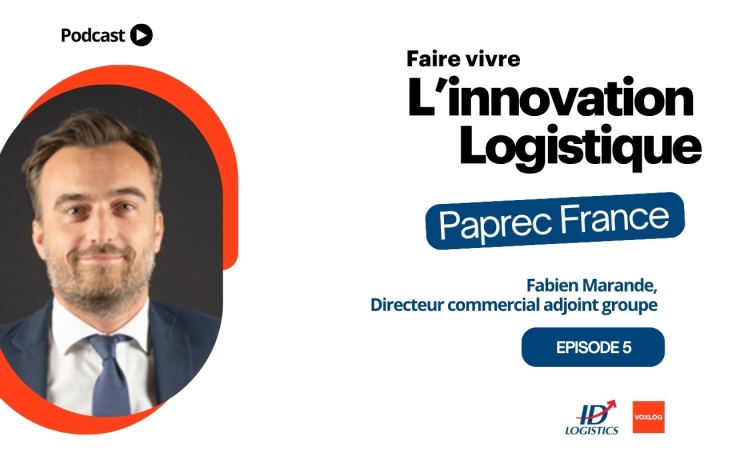